Advanced Techniques in Modern Tank Welding Inspection
Advanced Techniques in Modern Tank Welding Inspection
Blog Article

Comprehending the Relevance of Rigorous Tank Welding Assessment Processes in Preventing Failings and Enhancing Lifespan
In the realm of industrial operations, the importance of extensive storage tank welding assessment procedures can not be overstated. By executing different evaluation approaches, organizations can discover problems early, thus preventing costly repercussions and extending the life of their storage space containers.
Relevance of Welding Assessments
Acknowledging the vital function of welding evaluations in maintaining architectural honesty, these processes make certain that welds satisfy recognized standards and specifications - Tank Welding Inspection. Reliable welding examinations are extremely important in the building and construction and upkeep of tanks, as they straight affect the longevity and safety and security of the frameworks. By determining potential shortages, such as improper strategies or material problems, evaluations mitigate the danger of devastating failings
Welding examinations incorporate different techniques, consisting of visual exams, non-destructive testing (NDT), and assessments of welding treatments. Each method offers to verify the high quality and compliance of welds with sector regulations, therefore protecting both employees and environmental passions. Additionally, normal evaluations cultivate a culture of liability and excellence within the labor force, ensuring that all staff member stick to finest practices.
In addition, these assessments add to the overall lifecycle monitoring of storage tanks by determining wear or degradation early in the process. By addressing these issues proactively, organizations can expand the functional life-span of their assets, eventually causing set you back savings and improved integrity. In recap, the importance of welding assessments can not be overemphasized; they are essential for guaranteeing security, long life, and conformity in container construction and maintenance.
Common Causes of Tank Failures
Understanding the common sources of tank failings is crucial for preventing catastrophic occurrences and making certain the long life of storage systems. One prevalent root cause of tank failure is deterioration, which can considerably compromise the structural integrity of containers with time. Ecological elements, such as exposure to wetness, chemicals, and temperature level changes, can accelerate this procedure.
An additional vital element is improper welding strategies, which might result in defects like cracks or incomplete joints. These issues can endanger the storage tank's strength and bring about leakages or tears. Furthermore, poor maintenance practices can cause unnoticed damage, ultimately enhancing the danger of failure.
Layout defects, including insufficient thickness or poor product selection, can also contribute to tank vulnerabilities. Moreover, functional variables, such as overfilling or exposure to extreme stress, can strain the container beyond its desired restrictions.
Trick Evaluation Methods
Effective evaluation techniques play an essential role in minimizing the risks linked with container failures. A thorough method to container welding assessment involves numerous key methods, each made to identify prospective issues and site make certain structural stability.
Aesthetic inspection remains the first line of defense, allowing examiners to identify surface area abnormalities such as splits, rust, or imbalance. This strategy is often supplemented by non-destructive testing (NDT) techniques, which are important for evaluating weld top quality without compromising the storage tank's honesty.
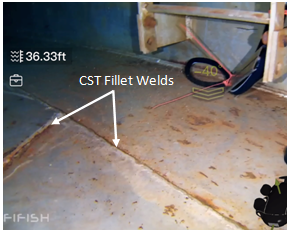
In addition, magnetic fragment testing (MPT) and color penetrant screening (DPT) work for detecting surface issues in ferromagnetic materials and non-porous surface areas, respectively. Each technique has its strengths and constraints; therefore, a mix of methods is frequently utilized to accomplish extensive assessment outcomes.
Advantages of Rigorous Inspections
While the immediate costs of rigorous inspections may seem difficult, the long-term advantages substantially outweigh these preliminary financial investments. Carrying out extensive assessment refines not just boosts the honesty and security of storage tank structures yet additionally reduces the threat of tragic failings that can lead to substantial financial losses and ecological damage.
Extensive examinations assist identify potential concerns early in the welding process, permitting for timely corrective activities that stop costly repairs or substitutes down the line. This aggressive method fosters a society of quality control, where adherence to finest practices becomes implanted in functional procedures. Normal evaluations add to enhanced property durability, as they guarantee that containers continue to be in optimal problem throughout their life expectancy.
On top of that, the paperwork produced from these examinations functions as an important source for maintenance preparation and performance evaluations. This data-driven approach can additionally enhance functional performance, bring about reduced downtime and improved performance. Eventually, extensive evaluations not just guard the architectural stability of containers but likewise give considerable financial benefits, reinforcing the concept that purchasing quality control is a sensible choice for any organization associated with container procedures.
Regulative Standards and Compliance
Regulative criteria and conformity advice are important parts of storage tank welding evaluation processes, as they establish the framework for guaranteeing security and top quality in procedures. Conformity with these standards not only reduces risks yet additionally boosts the total integrity of welded structures. Various organizations, including the American Society of Mechanical Designers (ASME) and the American Petroleum Institute (API), give standards that determine acceptable methods for welding, inspection, and testing.
These requirements mandate using qualified workers, the implementation of extensive evaluation procedures, and adherence to particular welding procedures. By aligning with regulatory requirements, companies can make certain that their containers meet the required safety and efficiency criteria, thus minimizing the possibility of devastating failures that can lead to substantial economic losses and ecological damage.

Additionally, regulatory compliance cultivates a culture of accountability and continual enhancement within the welding and construction sectors (Tank Welding Inspection). Normal audits and assessments guarantee that techniques stay aligned with advancing requirements, therefore promoting long-term dependability and operational effectiveness. Eventually, adherence to governing standards not just protects possessions but additionally boosts the life-span of welded containers, ensuring they offer their intended purpose efficiently over time
Conclusion
In final thought, extensive container welding examination procedures play a crucial duty in avoiding failures and extending the lifespan of storage frameworks. By recognizing possible deficiencies via different evaluation methods, organizations can alleviate risks linked with tank honesty.
Report this page