Pipeline Welding Inspection: Making Sure Conformity with Sector Requirements
Pipeline Welding Inspection: Making Sure Conformity with Sector Requirements
Blog Article
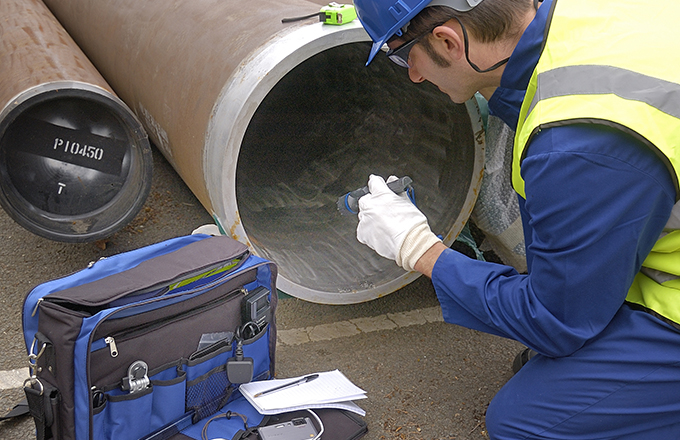
Ideal Practices for Pipe Welding Inspection: Methods, Criteria, and Treatments to Achieve High Quality Guarantee and Compliance
Efficient pipeline welding assessment is essential for making sure the honesty and safety of important infrastructure. By utilizing a mix of techniques such as visual examination and advanced non-destructive testing techniques, in addition to adherence to established market requirements like those from ASME and AWS, companies can significantly enhance their high quality guarantee procedures. However, the application of these finest techniques postures various challenges that warrant cautious factor to consider. Recognizing the intricacies associated with each stage of inspection is essential to attaining conformity and integrity in pipe systems. What specific strategies can be employed to navigate these obstacles properly?
Importance of Welding Inspection
The integrity of welded joints is paramount in making certain the safety and security and dependability of pipeline systems. Proper welding strategies and thorough inspection procedures are vital to stop failures that can bring about tragic occurrences, environmental damage, and death. Pipeline Welding Inspection. Welding evaluation serves as a preventative procedure, identifying defects such as splits, porosity, and incomplete blend prior to they escalate right into serious problems
In addition, pipeline systems often run under high pressure and severe problems, making the high quality of welds much more essential. Governing compliance is an additional significant aspect, as various standards dictate the quality control processes that need to be adhered to in pipe construction and upkeep. Failing to comply can lead to lawful ramifications and monetary losses.

The role of welding examination extends beyond plain verification of workmanship; it encompasses the assurance of lasting functional integrity. This includes an organized approach that consists of not just visual evaluations however additionally advanced non-destructive testing methods. Eventually, reliable welding examination is an investment in the longevity and security of pipe systems, guaranteeing they function as meant while decreasing threats connected with material deficiencies.
Key Inspection Techniques
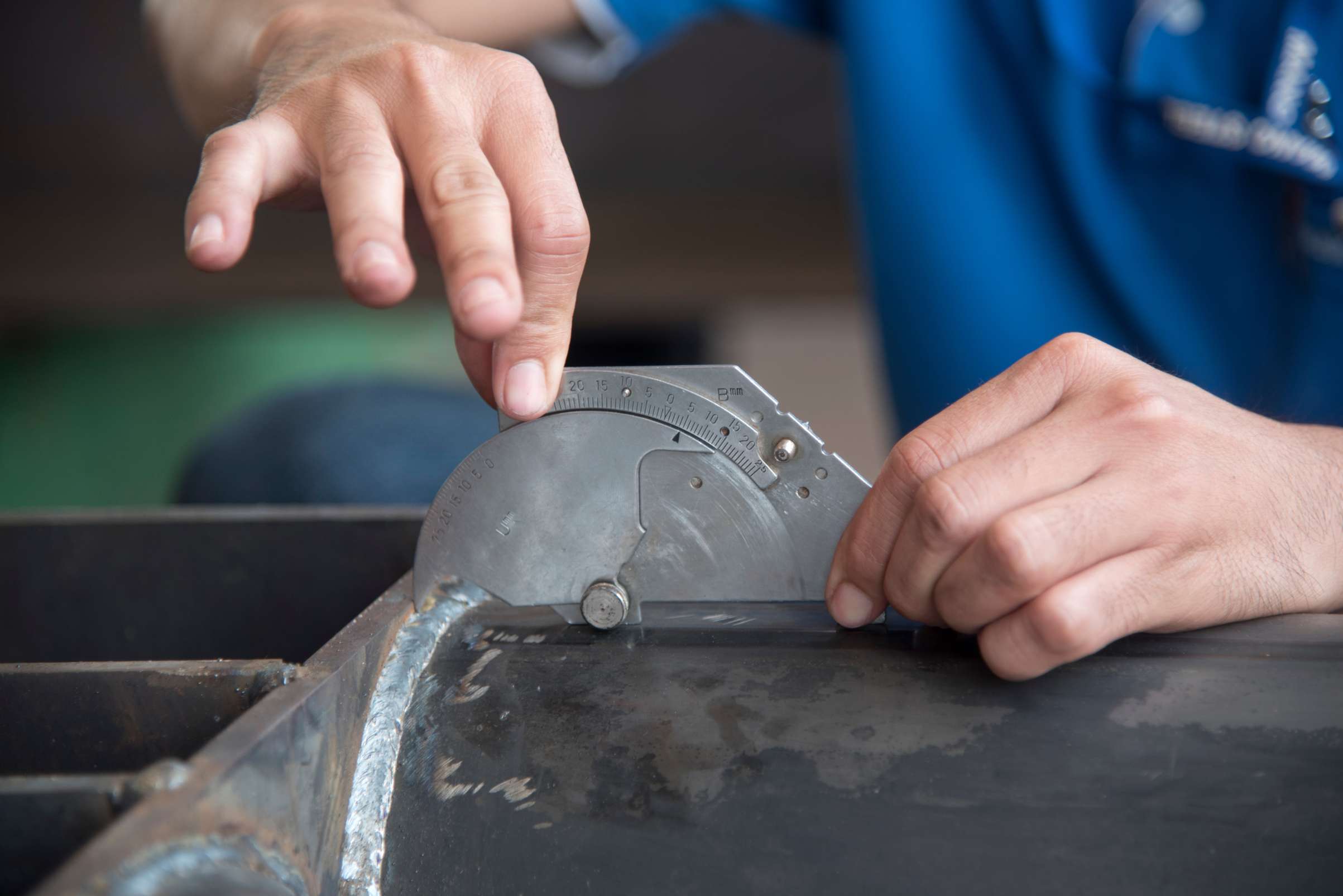
Visual assessment, frequently the initial line of defense, permits the recognition of surface flaws such as fractures, damages, and porosity. Ultrasonic testing utilizes high-frequency acoustic waves to detect interior defects, using an extensive assessment of weld stability. This non-destructive method is especially efficient for identifying discontinuities that may not show up externally.
Radiographic testing includes using X-rays or gamma rays to generate pictures of the welded joint, exposing interior issues. This strategy supplies thorough insights but may require specific devices and security factors to consider. Lastly, magnetic particle testing is efficient for finding surface area and near-surface discontinuities in ferromagnetic materials, utilizing magnetic fields and great iron bits.
Market Requirements and Rules
Compliance with industry standards and laws is essential for making sure the high quality and safety of pipe welding examinations. These requirements give a structure for finest practices in welding procedures, official source materials, and evaluation techniques, allowing companies to lessen problems and enhance the stability of pipeline systems. Trick bodies such as the American Society of Mechanical Designers (ASME), the American Welding Culture (AWS), and the International Organization for Standardization (ISO) set forth standards that are widely identified and embraced within the industry.
In the USA, policies from the Pipe and Hazardous Materials Security Administration (PHMSA) control the security of pipe operations, mandating rigorous inspection methods. These requirements not only serve to protect public security and the setting however likewise ensure conformity with legal and contractual responsibilities. Adherence to the relevant codes, such as ASME B31.3 for procedure piping, is crucial for maintaining functional effectiveness and regulatory compliance.
In addition, continuous updates and modifications to these standards show technical advancements and progressing sector practices, highlighting the need for organizations to remain informed and train employees accordingly. Eventually, durable conformity with established requirements cultivates trust and reliability in pipeline framework, guarding both stakeholders and possessions.
Efficient Examination Treatments
Effective inspection treatments are vital for identifying possible defects in pipe welds and ensuring the total stability of the system. A systematic technique to examination encompasses a number of key phases, including pre-weld, in-process, and post-weld evaluations. Each phase plays a crucial function in preserving quality control.
During pre-weld evaluation, it is important to evaluate the materials and joint configurations, guaranteeing compliance with project requirements. In-process examinations entail monitoring welding techniques and parameters, such as warmth input and take a Full Article trip speed, to avoid problems from occurring. This phase enables for real-time modifications to welding methods.
Post-weld evaluations include non-destructive screening (NDT) methods like radiography, ultrasonic testing, and magnetic fragment screening. These methods help detect inner and surface area defects that could endanger the pipeline's functionality. Documents of all assessment activities is paramount, giving a traceable document that sustains compliance with sector requirements.
Training and qualification of assessment personnel better improve the effectiveness of these treatments. By adhering to a structured examination procedure, organizations can minimize dangers, ensure conformity, and inevitably provide pipes that satisfy rigorous security and efficiency requirements.
Typical Challenges and Solutions
Pipeline welding examination provides several typical obstacles that can affect the top quality and safety of the end product. One substantial obstacle is the variability in welding strategies and products, which can result in irregular weld top quality. To address this, it is vital to establish standardized treatments and training for welders, making certain an uniform method throughout tasks.
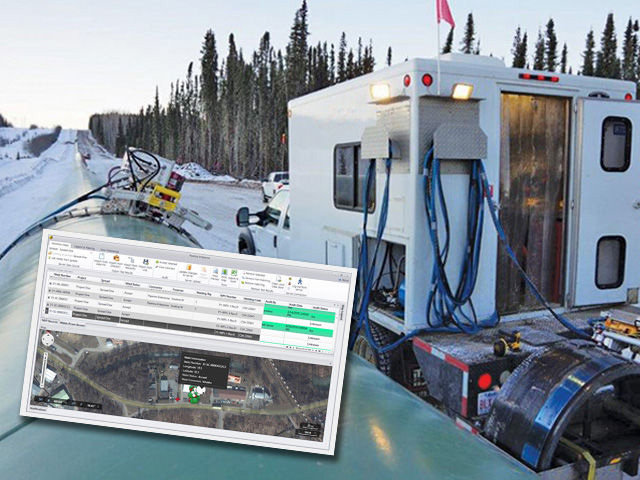
Environmental variables, including temperature level and moisture, can likewise affect the welding procedure, potentially bring about fractures or insufficient combination. Implementing controlled environments and sticking check my blog to pre-weld procedures can alleviate these risks.
Verdict
To conclude, the execution of finest techniques for pipeline welding examination is important for making certain top quality assurance and conformity with industry criteria. An extensive approach, integrating numerous techniques such as aesthetic, ultrasonic, and radiographic screening, helps with the recognition of defects throughout all phases of the welding process. Pipeline Welding Inspection. Adherence to established laws and effective assessment treatments not only improves the integrity and safety of pipeline systems however also reduces dangers related to welding defects, thus advertising total operational integrity
Compliance with sector criteria and regulations is important for making sure the top quality and safety of pipeline welding evaluations. These requirements supply a structure for ideal practices in welding processes, materials, and evaluation methods, enabling organizations to lessen flaws and boost the honesty of pipe systems.In the United States, laws from the Pipe and Hazardous Products Safety And Security Management (PHMSA) control the safety and security of pipe procedures, mandating strenuous examination methods. An organized strategy to examination incorporates numerous crucial stages, consisting of pre-weld, in-process, and post-weld assessments.In final thought, the implementation of best practices for pipe welding examination is necessary for making sure high quality assurance and compliance with industry criteria.
Report this page